We help you develop clear and actionable strategies to achieve your business goals, identify market opportunities, and stay ahead of the competition.
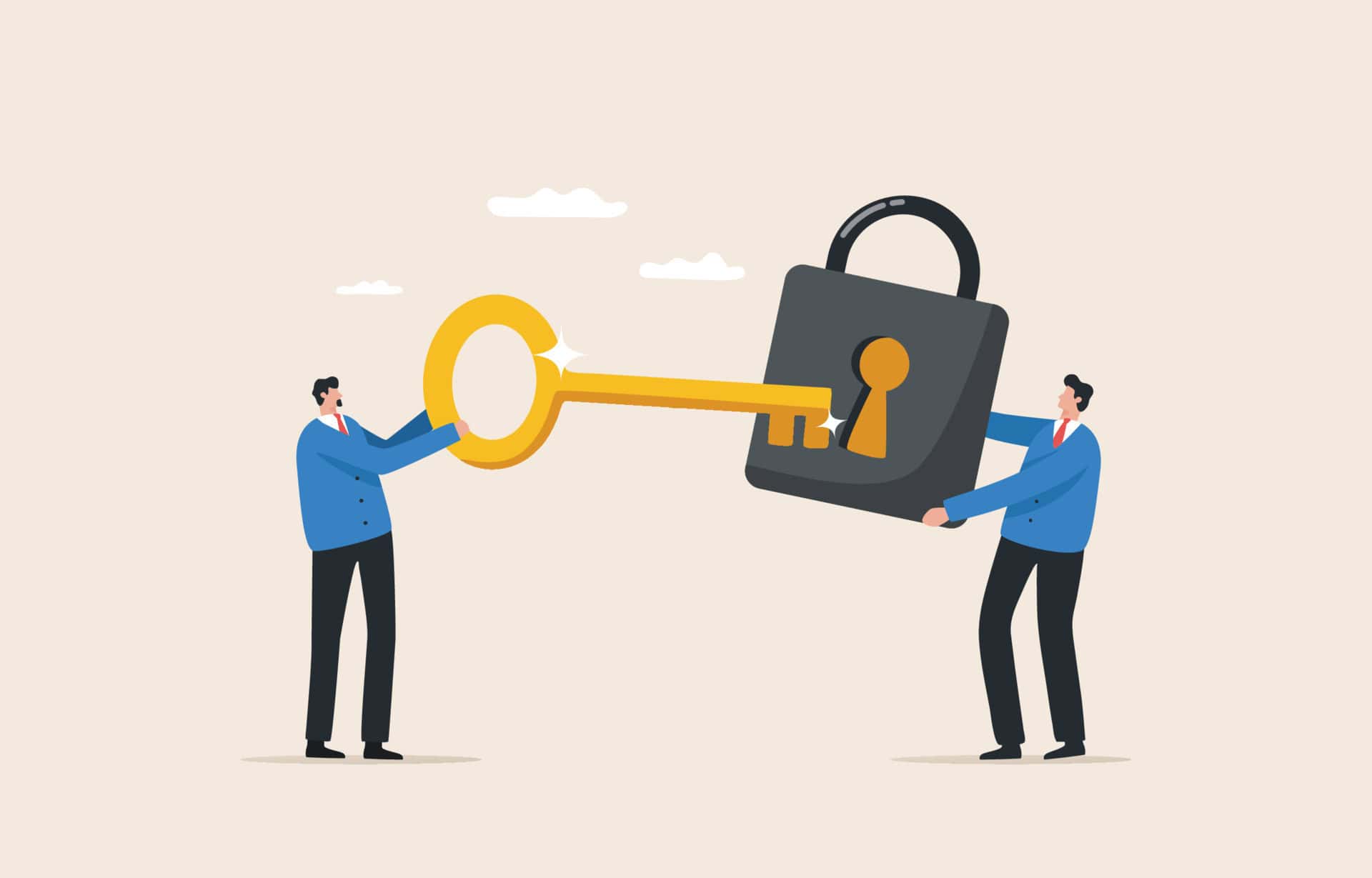
specialize in empowering businesses
We pride ourselves on delivering tailored strategies that drive growth and maximize efficiency. Our client-centric approach ensures personalized attention and seamless collaboration, resulting in measurable success for our partners. At KevinKennedyAssociates, we combine cutting-edge methodologies with a deep understanding of industry trends to deliver innovative solutions that propel businesses forward.
We help you develop clear and actionable strategies to achieve your business goals, identify market opportunities, and stay ahead of the competition.
Our experienced project managers ensure efficient execution of initiatives, delivering on time and within budget while maintaining quality standards.
We assist in optimizing your workforce by improving team dynamics.
We help you develop clear and actionable strategies to achieve your business goals, identify market opportunities, and stay ahead of the competition.
Latest Articles
Welcome to Daegu, the vibrant city that offers a plethora of 대구op (대구옵) choices for every adventurer. Whether you’re seeking thrilling activities or premier experiences, Daegu has it all. Let’s dive into the top spots where you can immerse yourself in unforgettable moments and create lasting memories.
Welcome to the exciting world of Gangnam Mirrored Rooms, where you can experience the vibrant and thrilling Korean nightlife scene. Located in the heart of Gangnam, these unique venues offer a one-of-a-kind entertainment experience that you won’t find anywhere else. From live performances to dancing and music, Gangnam Mirrored Rooms … Read the rest
Welcome to our safe outcall services that come with no upfront fees. We understand the importance of providing a secure and comfortable experience for our clients. Therefore, we offer 선입금 없는 출장, which means you don’t have to worry about making any prepayments. With our services, you can